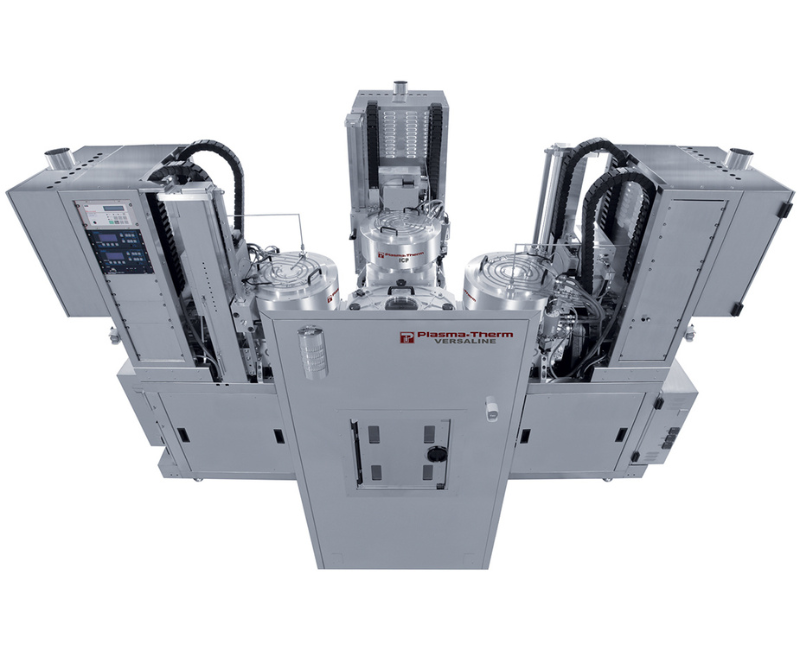
VERSALINE®
OUR VERSALINE PLATFORM IS THE WORKHORSE FOR A VARIETY OF APPLICATIONS IN SPECIALTY SEMICONDUCTOR MARKETS
VERSALINE system models are configured to perform an array of etch and deposition processes. Ion beam technology suits a range of applications, from low, controllable damage etching to high-rate, high-aspect-ratio, deep silicon etching to difficult materials. The systems support process control through EndpointWorks®. Enhancements include data logging, automated maintenance scheduler (AMS), and SECS/GEM. Our Cortex® control system provides a stable, user-friendly control interface designed for efficiency and productivity.
The VERSALINE platform’s modular design allows for flexible configuration of substrate handling for a variety of handling options, from R&D single wafer or carrier loading with a loadlock to high-volume, multi-chamber production clusters. Clear upgrade paths that leverage costs and process development make future planning easy.
Other features include:
LL
Loadlock for single substrate or single batch carrier. Upgradable to cassette loading.
CX
For cassette and cluster configuration (up to 75mm to 200mm capable)
Our VERSALINE ICP etch platform results from decades of technological evolution at Plasma-Therm®.
Process
- High flexibility for application optimized processes (e.g., from slow, controllable to high-rate throughput maximized; profile control from sloped to vertical)
- Large library of processes for wireless, photonics, power device, compound semiconductor, memory, quantum, and advanced packaging applications (material specs available upon request)
- II-VIs and III-Vs (GaAs, InP, GaN, AlN, CdTe, InSb)
- Silicon-based (Si, poly-Si, SiC)
- Dielectrics (SiO2, SiNx, SiON, quartz, fused silica)
- Polymers (PR, PI, BCB)
- Metals (Al, Cr, V, W, Mo, Ti, Ta, Nb, Cu, Au, Pt)
- Metal oxides and nitrides (TiN, TaN, TiOx, TaOx, HfOx)
- Piezoelectrics (LiNbO3, LiTaO3)
- Corrosive chemistry (HBr, Cl2, BCl3) supported with “armored” corrosion-resistant components
Hardware
- Flexible and configurable handling cassette cluster systems to single-substrate loadlocks
- 2MHz ICP source: heated for process stability, decreased first wafer effects, and increased MTBC
- 13.56MHz and optional 40MHz substrate bias
- Substrate temperature control with backside helium using mechanical or electrostatic clamping
- Application-specific substrate electrode temperature ranges
Software
- Cortex control system
- EndpointWorks program supporting laser, optical emission, and other system parameter-based endpoints
Our VERSALINE system Deep Silicon Etch (DSE) technology delivers deep reactive ion etching (DRIE) of silicon with profile control and sidewall smoothness utilizing award-winning fast process control. Outstanding process flexibility and latitude are offered with the highest selectivity to mask material in the industry.
Winner of the MicroNano Award for “Most Innovative Technology.”
Process
- High aspect ratios
- Smooth sidewalls
- High uniformity
- High selectivity
- Notchless SOI
- Profile control
- Optimized etch rates
- Aspect ratio dependent etching (ARDE) reduction
Hardware
In addition to the features and benefits available with VERSALINE ICP, the VERSALINE DSE offers:
- Smooth sidewall with short process step times (including fast gas switching, pressure control, and RF matching)
- Notchless silicon-on-insulator etching (patented) with bias control and endpoint algorithms (patented)
- Aspect ratio dependent etching (ARDE) reduction (patented)
Software
- Cortex control system
- EndpointWorks program supporting laser, optical emission, and other system parameter-based endpoints
Our VERSALINE RIE systems are installed in facilities ranging from R&D to high-volume production. VERSALINE RIE offers low maintenance and high versatility for multiple applications. Multiple substrate sizes are conveniently accommodated without hardware reconfiguration. Available upgrades to ICP and cluster configuration.
Process
- Extensive process library
- Wide process latitude
Hardware
- Flexible substrate bias with 13.56MHz and optional 40MHz
- Up to 200mm wafer capable
- Improved preventive maintenance cycles with thermally managed chamber liner and pump train
- Application-specific electrode temperature ranges available
- Process specific electrode material
Software
- Cortex control system
- EndpointWorks program supporting laser, optical emission, and other system parameter-based endpoints
Our IBE technology on the VERSALINE system incorporates high-performance large-area ion sources and advanced motion control for industry-leading process results, best-in-class uniformity and throughput, and lowest cost of ownership. Marathon grids™ technology is the key enabler to its verified performance.
Process
- “Difficult” materials (noble metals, ScAlN, PZT, LTO, LNO)
- RIBE (reactive ion beam etching)
- <2% 3-sigma (200mm)
- Data storage, advanced memory, quantum applications
- Profile control with wide-range tilt angles
Hardware
- Cluster combinations (up to 3 modules) or single process module configuration
- Process 200mm wafers, 150mm wafers, and 9.5-inch pallets; scalable to 300mm
- Advanced motion controls that provide up to 40% higher throughput
- Wide energy range—ultra-low to high power
- Long-life Marathon grids provide up to three times longer life than standard grids
- Higher yields through precision tilt and rotation
- Programmable virtual shutter
- Scanning motion available with optional planetary configuration when ultra-high uniformity is required
Software
- Cortex control system
- EndpointWorks program supporting SIM
Our IBD systems, whether configured for R&D or production, deliver best-in-class uniformity and throughput and the lowest cost of ownership. Marathon grids technology is the key enabler to their verified performance. Marathon grids can be installed on existing systems to improve performance and gain two times longer life or better.
Process
- Optical films, data storage, magnetic transducers, advanced memory, quantum applications
- <2% 3-sigma (200mm) and all tilt angles available
- RIBD (reactive ion beam deposition)
- Stoichiometric and sub-stoichiometric oxides
Hardware
- Cluster combinations (up to 3 modules) or single process module configurations
- Process 200mm wafers, 150mm wafers, and 9.5-inch pallets; scalable to 300mm
- 6 or 8 target configurations with enhanced inter-target shielding
- Advanced motion controls provide up to 40% higher throughput than legacy ion beam systems
- Long-life Marathon grids provide up to three times longer life than standard grids
- Programmable virtual shutter
- Wide-range tilt angles
- Assisted IBE with secondary ion gun
Software
Our VERSALINE PECVD results from decades of technological innovation. VERSALINE PECVD systems can deposit many different high-quality films, ensuring you get maximum, reliable high productivity at a low total cost of ownership.
Process
- Silane-based films (a-Si, SiO2, SiNx, SiON, SiC, SiOF, a-SiC)
- TEOS films
- Stress control
- High and low deposition rates
- Tunable refractive index
Hardware
- 13.56MHz standard with additional optional low frequency
- High-temperature electrode up to 500C
- 100mm to 200mm substrates
- Remote plasma cleaning option for shorter clean cycles
Software
- Cortex control system
- EndpointWorks program using OES for cleaning
Our VERSALINE HDPCVD platform offers dense films at low substrate temperatures. The system utilizes a high-density ICP plasma with the capability to fill trenches and holes.
Process
- Silane-based films (a-Si, SiO2, SiNx, SiON, SiC, SiOF)
- <180C deposition conditions
- Trench/gap fill
- High-density, low-BOE films
- TEOS and DLC (diamond-like carbon)
Hardware
In addition to the features and benefits available with the VERSALINE ICP, the VERSALINE HDPCVD offers:
- Substrate temperature control with backside helium and mechanical clamping
- Low-particulate processing environment with thermally managed reactor design—up to 180C for electrode, walls, and showerhead
Software
- Cortex control system
- EndpointWorks program supporting laser, optical emission, and other system parameter-based endpoints
The VERSALINE Large-Area PECVD platform provides a cassette-to-cassette batch solution for high-volume production. The LAPECVD provides the thousands of wafer passes per month to meet demanding production capacities. When coupled with optional in situ deposition rate and film thickness metrology, run-to-run thickness is enhanced.
Process
- Stress control
- High uniformity
- Tunable index
Hardware
- Dual cassette-to-cassette handling
- Multi-substrate batch processing
- Platen heating up to 350C
- RF power at 13.56MHz with optional low frequency
- Thermally managed reactor design—up to 175C for internal walls and showerhead
Software
- Cortex control system
- EndpointWorks program supporting optical emission, optical emission interferometry, and other system parameter-based endpoints
Unlike conventional photoresist strip systems, we utilize high-density radical flux (HDRF) technology, which produces high concentrations of reactive radicals without charged particles or unwanted photons. This chemical (non-physical), non-damaging plasma is ideal for conventional and low-temperature applications.
When placed on the VERSALINE system in a cluster configuration, the HDRF provides a plasma strip or surface treatment following another plasma process.
Process
- Low temperature
- No device damage
- Downstream processing
- Resist strip, surface modification, post DSE polymer removal, sacrificial layer removal
Hardware
- Wide temperature range (80C to 250C)
- 50mm to 200mm wafer sizes
- Distributed ICP 13.56MHz sources
- Optional water vapor delivery system
Software
- Cortex control system
- EndpointWorks program supporting optical emission and other system parameter-based endpoints
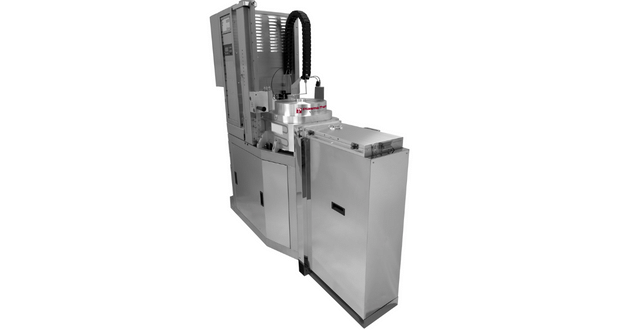
Title for image
CONTACT A PRODUCT SPECIALIST
NEED ASSISTANCE?
Let our experts help you customize our processes solutions for your applications.